When a bearing in your heavy equipment fails prematurely, the impact can be devastating. Safety can be jeopardized and contaminants may invade your fluid systems, setting the stage for component failure, unplanned downtime, lost production and high repair costs. You can reduce the risk of bearing failure by learning why it happens and how to prevent it.
WHY BEARINGS FAIL
All bearings wear out over time, but there are ten common reasons why they fail at low hours.
- OVERLOADING. Working long hours in high-load applications can cause bearing lubricants to generate excess heat and lose viscosity. As the lube film gets thinner, contact between the bearing’s key components increases, accelerating wear and increasing the odds of an early failure.
- IMPROPER LUBRICATION. Several lube-related problems can have a negative impact on bearing life. One problem is using the wrong lubricant (one that doesn’t comply with the manufacturer’s recommendations)—putting engine oil in the final drive compartment, for example. Other problems can arise when lubricant is not maintained at the proper level or the manufacturer’s guidelines for fluid and filter changes are not followed. Whether the issue is type, quantity or cleanliness of the lubricant, the effect on bearings is largely the same: improper lubrication causes accelerated wear and premature failure.
- CONTAMINATION. Contaminants can be introduced in many different ways—at assembly, during operation or while a product is being serviced. Contaminants are also generated internally as components work and wear. Regardless of the source, when contaminants come into contact with bearings, the risk of premature failure increases significantly. Bearings that have been subjected to contamination can be scratched, scored, pitted, grooved, bruised, rusted or exhibit a matte or satin finish.
- DISTORTION. Bearing components lose their original shape when they’re forced onto a housing or shaft that’s out of round or when they’re installed improperly. The resulting distortion increases the risk of an early fatigue failure.
- MISALIGNMENT. It is virtually impossible to achieve perfect alignment between a bearing and the housing or shaft upon which it’s installed. Excess misalignment can be caused by design deficiencies, installation errors or shock loads and other stresses that occur during machine operation. Although bearings are designed to accommodate a certain level of misalignment, exceeding that level causes uneven load distribution, which paves the way for failure.
- IMPROPER FIT. Choosing the right-size bearing for a given application is critical. An improper fit—whether it’s too loose or too tight—impedes bearing performance and reduces life. Signs of a poor fit include split races, fretting corrosion and creep wear. Additionally, bearings are designed to align mating parts, like gear sets. When the wrong-sized bearing is used, mating gears will be misaligned, causing premature gear failure, which results in higher repair costs and unplanned downtime.
- VIBRATION. Excess vibration can compromise bearing life, especially in low-speed, high-load applications. A high-quality cage, made from brass or a nonmetallic material, helps minimize the effects of vibration-related problems.
- MATERIAL DEFECTS. All bearings are not created equal. Those made from ultra clean steel, using the latest manufacturing and heat-treating processes, are less likely to contain material defects that jeopardize performance and life. Material flaws are more prevalent in lower quality bearings, but in most cases, only a metallurgist can detect the defects.
- IMPROPER SERVICING TECHNIQUES. There are many ways to cause bearing damage in the service shop. One common mistake is using the wrong tools, particularly wooden mallets. This often leads to an improperly installed bearing, causing misalignment of the bearings and mating parts. Another improper service technique is removing a bearing with a flame cutter or by shrinking the outer race with a weld bead. Heat from the flame cutter or weld will alter the metal structure and heat treat, softening the bearing. A third mistake made in the service shop is using compressed air to spin a bearing dry. Spin-drying leads to metal-to-metal contact, causing wear prior to installation.
- ELECTRICAL CURRENT. When a weld is grounded in the vicinity of a bearing, the electrical current can pass through the bearing, causing arcing and burning at the points of contact between the races and rollers. This may produce a single burn or multiple grooves. The result is often excess noise and reduced service life.
Special CTA Headline Here
sample button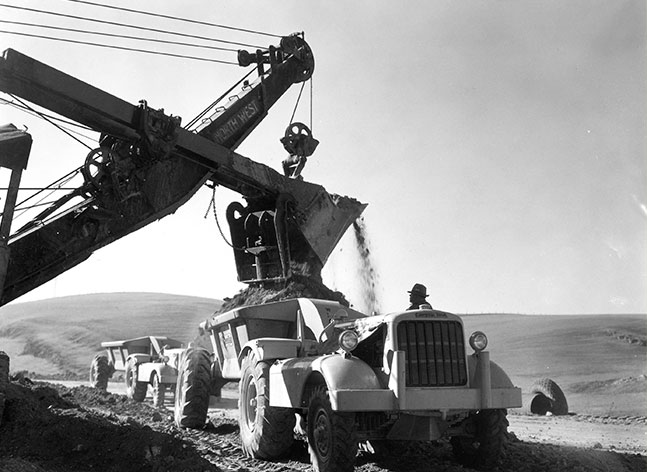
HOW TO PREVENT PREMATURE BEARING FAILURES
Knowing why bearings fail at low hours is important, but it’s also critical to understand how to prevent premature failures. Here are five ways to do that.
- FOLLOW LUBRICATION RECOMMENDATIONS. Caterpillar makes recommendations on the type and quantity of lubricant to use, as well as the proper lube intervals. For best results, stick to that plan.
- GET YOUR FLUIDS ANALYZED. Regular fluid analysis allows you to detect the presence of bearing-related contamination early, so you can spot potential problems and resolve them before failure. Enrolling in a comprehensive fluid analysis program is one of the best things you can do to get dependable performance and long life from your bearings and your entire machine.
- PERFORM REGULAR INSPECTIONS. Bearings need to be removed, cleaned and inspected periodically to check for damage or excess wear. Follow the procedures outlined in your service manual and always use recommended tools. Fortunately, there are some specific things you can do. Remove bearings carefully, avoiding harmful procedures like flame cutting. Handle bearings with clean dry hands, or wear clean canvas gloves. Clean bearings with the recommended solvent; dip them in clean oil; hold their inner and outer races together while you blow air through them to dry. Examine bearings carefully, inspecting all surfaces and rolling components. Replace bearings that are brownish-blue or bluish-black in color. Replace bearings that have damaged or worn seals or shields. Replace bearings with signs of cracking, pitting, scratching, flaking or other surface damage. If you don’t see signs of wear or damage, lubricate the bearing lightly and turn the outer race slowly. Never spin it. If the bearing clicks or sticks, clean it again and turn the outer race another time. Replace it if the clicking or sticking persists. If the bearing shows no signs of wear or damage and has low hours, it can normally be reused. A high-hour bearing should be replaced, even if it looks perfectly fine. There’s no reliable way to assess fatigue life, so don’t take chances reusing a bearing that could be in its final hours. If you’re not installing the bearing immediately, oil it; wrap it in clean, oil-proof paper; place it in a box and store it in a dry, dust-free place.
- CONTROL CONTAMINATION. There are dozens of opportunities to introduce contaminants into your systems while you’re working, maintaining and servicing your machine. You can reduce the risk of contamination if you’re willing to work at it. Make sure anyone who’s involved with maintenance or service receives contamination control education. Teach people to handle parts properly—with clean dry hands and no dirty rags. Clean up the work environment and storage areas. Adopt cleaner fluid storage and transfer processes. Control operating temperature to reduce internal wear. Fix leaks and replace worn seals promptly. Talk to your equipment dealer about other ways to control contamination in your operation.
- BUY THE RIGHT BEARINGS. At replacement time, don’t be tempted to buy the cheapest bearings on the shelf. Invest in a high-quality product—whether you’re replacing a specialty bearing or a standard model. Choose bearings made from the best steel, using the latest heat-treat technologies and precision-manufacturing processes. If you pay a little more for your bearings now—and maintain them properly—you’ll see the benefits in the future, in terms of higher performance, longer life, more uptime and lower repair costs.